The knowledge factory: Lean meets personal knowledge management
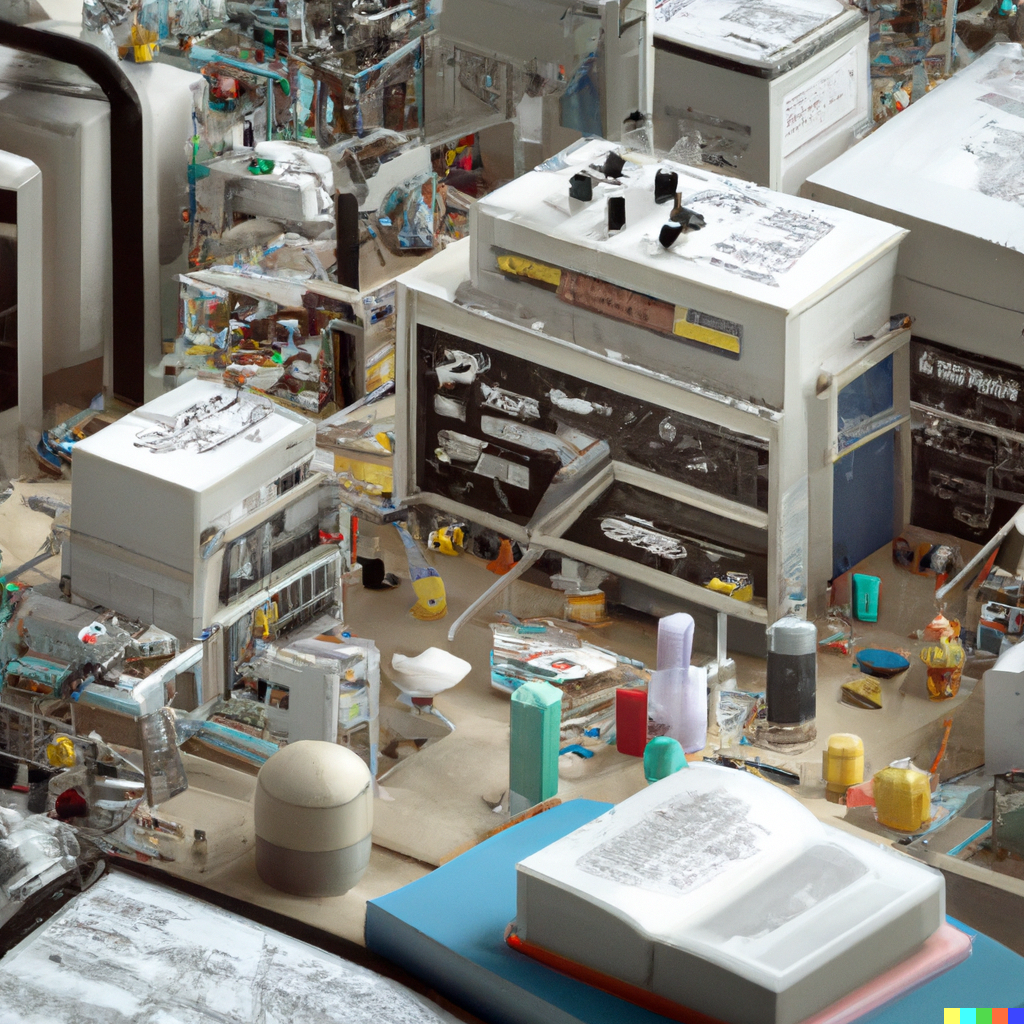
We all consume information and somehow store it (bookmarks, screenshots, save a pdf, etc.) yet we forget what we consume or never use it again. To tackle this problem I decided to enroll in Building a second brain course by Tiago Forte. Even though I had been using a part of the concepts for over 2 years, I felt something wasn’t clicking yet. That lead me to pay 950€ for an online course lasting 1 month, which is not a small investment.
Is it worth it? I think so, but I haven’t unveiled its full potential yet. It should be more obvious as time passes and the system compounds. So far the course has helped me, and is still helping in taking control of what I consume, making it much easier to produce content and creating a mindset change. I consider that whenever something challenges your way to see the world it is positive.
What is PKM?
Building a second brain is a modern take on Personal Knowledge management. As the name suggests it uses digital tools to offload knowledge and using it when needed. Something that has surprised me is the huge number of analogies I can see between the course and Lean manufacturing methodologies.
To put you in context, I am an engineer that spent 3 years working as a Lean manufacturing expert. I was responsible for two Lean initiatives in Tallinn, Estonia, and implemented a Lean culture and continuous improvement initiative in two factories, in Spain and in France. Revisiting Lean concepts for digital organization felt refreshing.
The goal of this article is to show that the core concepts for PKM from the course are heavily based in Lean and, I am attempting to explain those by using clear examples.
PKM comprises of 3 different levels according to Tiago:
Level 1: Storing information
The first level is straight forward. If you want to come back to a piece of information in the future you need to store it. Consider the information as our inventory. In this case, more is worse. We can link this to one of the key wastes in Lean: inventory. The definition of inventory goes as follows: inventory is everything that doesn’t add value.
Everything that we save involves a cost (both mental or physical). If we decide to save something, the possible value of it needs to be greater than the cost of saving it. Remember that value is only added when the inventory is sold or used. So in this case for digital notes, the value doesn’t come from storing the information but from using it. Digital notes are the warehouse we will use for new projects, and we don’t want to store pieces that we won’t use. Increasing inventory adds extra problems. In a factory we run out of space. However for digital notes, read-later apps or bookmarks there is no limit usually. But having too much inventory involves extra searches done and time reviewing “useless notes” to find what we want.
Yes, I know everything is “potentially useful”. I have done this mistake many times. One of the tasks in the course is to archive everything in a folder. It has been eye-opening to realize, that most of the things I moved to the archive I haven’t felt the need to check again. If you are having problems with this, create a clear list of active projects, interests, and responsibilities to make it easier to understand what is relevant for you and worth saving. Save only what will be useful, since notes don’t add value until used.
Level 2: Managing knowledge
So we have covered slightly the importance of thinking what to store. The next question is where to store it? Welcome to the P.A.R.A method. It is a 4-level folder structure: Projects, Areas, Resources, and Archives. For more information on this check the PARA blogpost from Tiago’s webpage.
One of the main points of this is to divide information by actionability. This resembles the 5S Lean methodology, which involves 5 steps (Sort, Set in order, Shine, Standardize, and Sustain). First you need to take everything you have, put it into different boxes depending on how often you use it: put the things you use most nearby, the things you use often within reach. The things you sometimes use don’t need to be close. And at last get rid of what you don’t use. Then do regular cleaning and sustaining. Repeat the circle yearly.
You have what you need in place, what is the next step? Labeling and instructions. You need to understand what each thing you have is. For digital notes, the equivalent of labels are not tags, but Progressive summarization. It involves bolding the text, highlighting the bolded text, and then a small summary on top. This provides a rich description and context of the note to quickly understand the note in a glimpse. And those summarized notes will be the Work In Progress for your projects.
Making things visual is also a big part of Lean:
“Use visual control, so that problems are not hidden” - The Toyota Way
These previous tools help with the visuality, if you have a list of active projects, it makes it easier to understand what is active and needs work and it helps you put the rest aside. The summarized notes will make it visually appealing to direct your attention to what’s “important”. Having the same P.A.R.A folders across apps and platforms (extra points for adding emojis) helps with the visuality and standardization, thus making you somehow software agnostic.
Level 3: Enabling action
We now have a part of the Work In progress in the form of summarized notes. Because we are saving what we consider important over time, whenever we need to jump into a project we have something to start with.
“I hear and I forget, I see and I remember, I do and I understand.” - Unknown
This might be the biggest challenge. We are used to consuming rather than producing. It is scary to put something you have made out there. “What people will think”, “I am not good enough”, “I don’t have anything to offer to others” etc. will hunt you and try to persuade you not to create. And even if you don’t have those fears, you might still encounter problems trying to start a certain project.
Introducing overproduction, overproducing is the biggest sin in lean manufacturing since it might create all the rest of the wastes (we produce something we don’t need -> Store in a warehouse -> Wait -> Search when needed, it is outdated-> Rework. Waste all the way).
So we can say that overproducing is producing more than needed or before needed. It is key to produce only when needed, using Just In Time. The definition of value can change over time. So make sure you do what is needed only when needed. Share often to receive feedback.
“There is nothing as useless as doing efficiently that which should not be done at all.” - Peter F. Drucker
Getting feedback early can help you stay on the right track in early phases without doing “wrong work” that will need rework. Another added benefit of sharing a draft: the feedback is relevant as people don’t tend to focus on small insignificant details and overall looks. Focus shifts to the actual concept or direction of the work. Combine this with both learning and an open mindset and you are up for a winning strike.
Overproducing in a specific project means that you are increasing the lead time since you are doing more than you need. When you apply this to multiple projects the phenomena amplifies and it will take you longer to start another project. Imagine that your colleagues do the same. Result: Things take a long time to finish. When waiting for a long time to retake a project you risk losing the mental state you were in, and it makes retaking it more difficult. A key tool for that are the intermediate packages. Semi-finished parts of work that let you come back to a project easily: a summary, a table, a diagram, documentation, etc.
Getting to the flow state has multiple requisites. There is an environment setup (the room is okay, phone in silence), mental setup (convincing yourself), and emotional setup (convince yourself that you can do it). Use the intermediate packages to enable changing projects and getting to the flow easily. This has the added benefit, that since it is easier to change projects you can just do small pieces of work for each project and thus reduce lot size.
Let’s draw the lean manufacturing analogy by using an example. Imagine that it takes 2 hours to change from producing product A to product B in a complicated machine. At the moment we are producing a single product per day, and we have 4 products in total that we sell. Because we wait one day to change a product, we need to have inventories in case somebody orders another product, since we cannot produce it the same day. But imagine that suddenly we can reduce the setup to 30 minutes. With the time it used to take us to do 1 product changeover we can make 4 product changeovers, and produce 4 different products in a day. We can reduce our inventory a lot, and only produce when there is an order. You are now much more flexible.
Move fast, touch slightly to be able to work in multiple things at the same time without batching. When working with teams that apply the same concepts everything is faster. And look for simplicity, not perfection.
I hope it is clear why we need to make projects interruption-proof and smaller.
Finally to enable action, we need to show the work we have clearly. The project list should be up-to-date to give an understanding of what are we working on at any specific moment. How can you otherwise have an understanding of where you should spend your time? In Lean manufacturing, the Kanban cards are used to visualize the workload and queues.
“Commitment without understanding is a liability” - Oliver Wight
Final thoughts
We should learn from Lean manufacturing that problems are opportunities. Japanese lean companies aren’t satisfied when they can’t see problems. No problems means that you are not able to see them. And when we can see the problems then we can solve them. Which is done by reducing lot sizes or inventory levels until new problems surface. The fragility of the system is a part of the goal since it helps us to improve constantly.
You might not even need to look much into the future to do your job:
“I learn each day what I need to know to do tomorrow’s work” -Arnold Toynbee
Revisiting what I have learned in the course through Lean concepts clarified how Lean can help our Personal Knowledge Management and Project Management.
Get rid of the excess and focus on what is important. Save what you need. Do what you need. Improve continuously.
Happy to see you at the end of the article :)
If you liked it, consider subscribing to my newsletter, where I refine notes and bookmarks from my personal knowledge management system and share it with the world.